How It’s Made / PART 1: The Deposit and Mining
Welcome to Part 1 of our three-part series, "How It's Made," where we will explore the complex process of mining and producing the industrial-grade kyanite that refractory engineers worldwide have come to rely on.
From start to finish, creating Virginia Kyanite takes one to two months. The process involves more than twenty-five meticulous beneficiation steps, and employs literally tens of tons of heavy duty machinery, lots of manpower, and rigorous quality control techniques to accomplish.
In this first installment, we shed light on our source mines at Willis Mountain and East Ridge in Dillwyn, Virginia, and the process of mining these world-class ore bodies.
To understand how Virginia Kyanite is made, we must first explore where it comes from:
Finding a Source
The first requirement for mining and refining industrial grade kyanite is to find a source mine that meets specialized criteria: silica and alumina, the two most abundant oxides on Earth, must be present in specific ratios (that have been subjected to the necessary geological heat and pressure) to form the sillimanite family of minerals; the ore deposit must be large enough to be economically viable; and the deposit must be low in contaminants.
Willis Mountain from the North.
Willis Mountain and East Ridge:
This meticulous sourcing and vetting process led us to establish our cornerstone of operations in the heart of Dillwyn, Virginia at Willis Mountain, which has graced us with some of the world's finest mineral deposits for more than 75 years and counting.
Seventy miles west of Richmond and fifty miles south of Charlottesville, the Willis Mountain deposit resides in the geological occurrence known as the Whispering Creek Anticline. The deposit is made up of two exposures: Willis Mountain itself and East Ridge, comprising the other half of the anticline.
Willis Mountain is a world-class deposit that has been continuously mined since the 1950s. The mountain remains over 50% untouched, showcasing its vast potential. Substantial reserves are also present at East Ridge, where mining began in the late 1970s.
East Ridge Plant and Quarry.
Geological Origins:
Willis Mountain's formation, dating back 465 million years to the Middle Ordovician Period, involved the venting of mineral-rich fluids that deposited clay minerals. Willis Mountain’s ore body consists of kyanite-quartzite rocks (containing 20-30% kyanite and impurities: quartz, several varieties of mica, iron oxides, iron sulphides, and minor minerals), and rises 475 feet above the surrounding countryside. The East Ridge deposit is similar, running 1.75 miles and rising 300 feet.
While the lifetime of these two Virginia deposits hasn’t been definitively determined, there is enough economically viable ore to continue mining for multiple generations at current production rates.
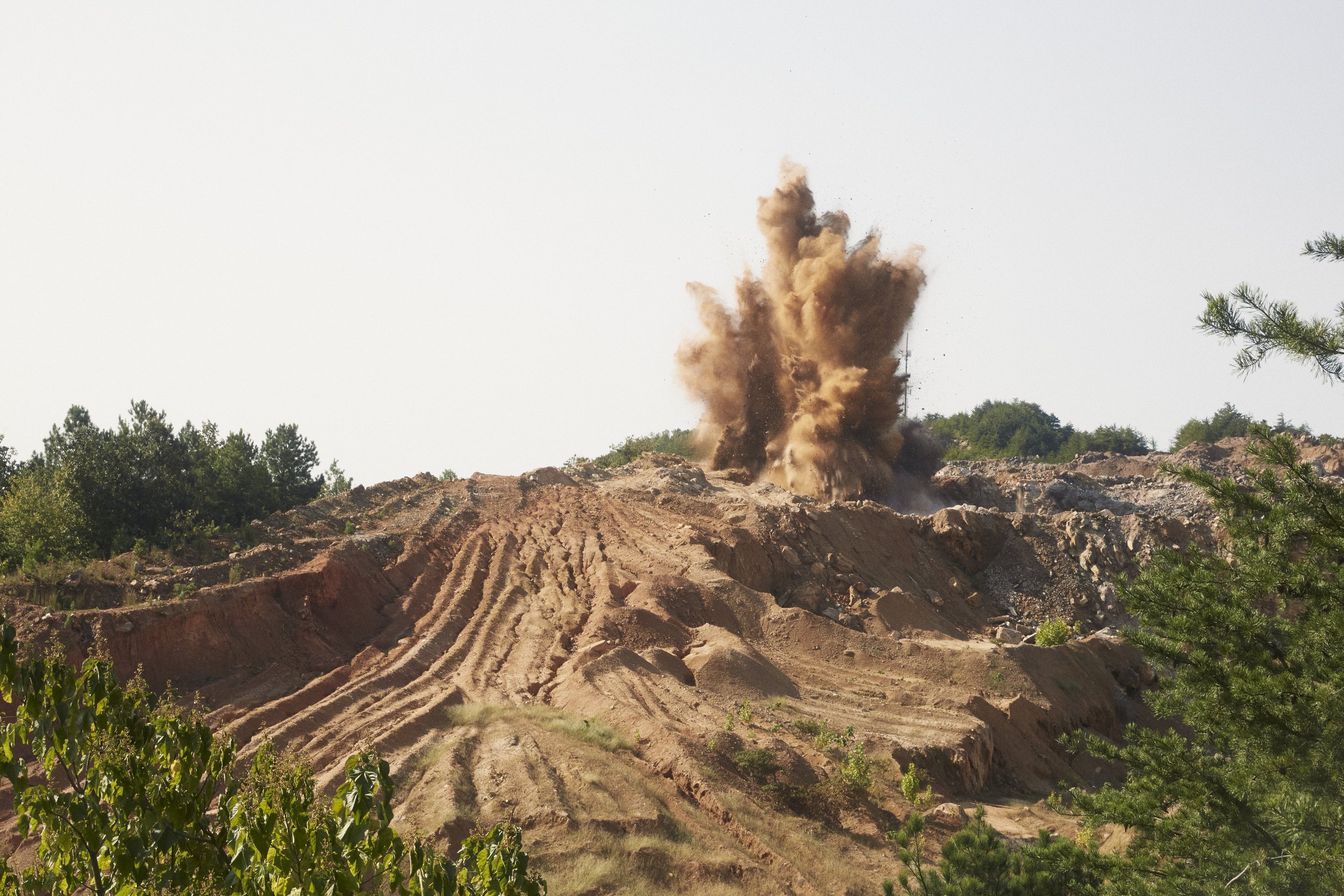
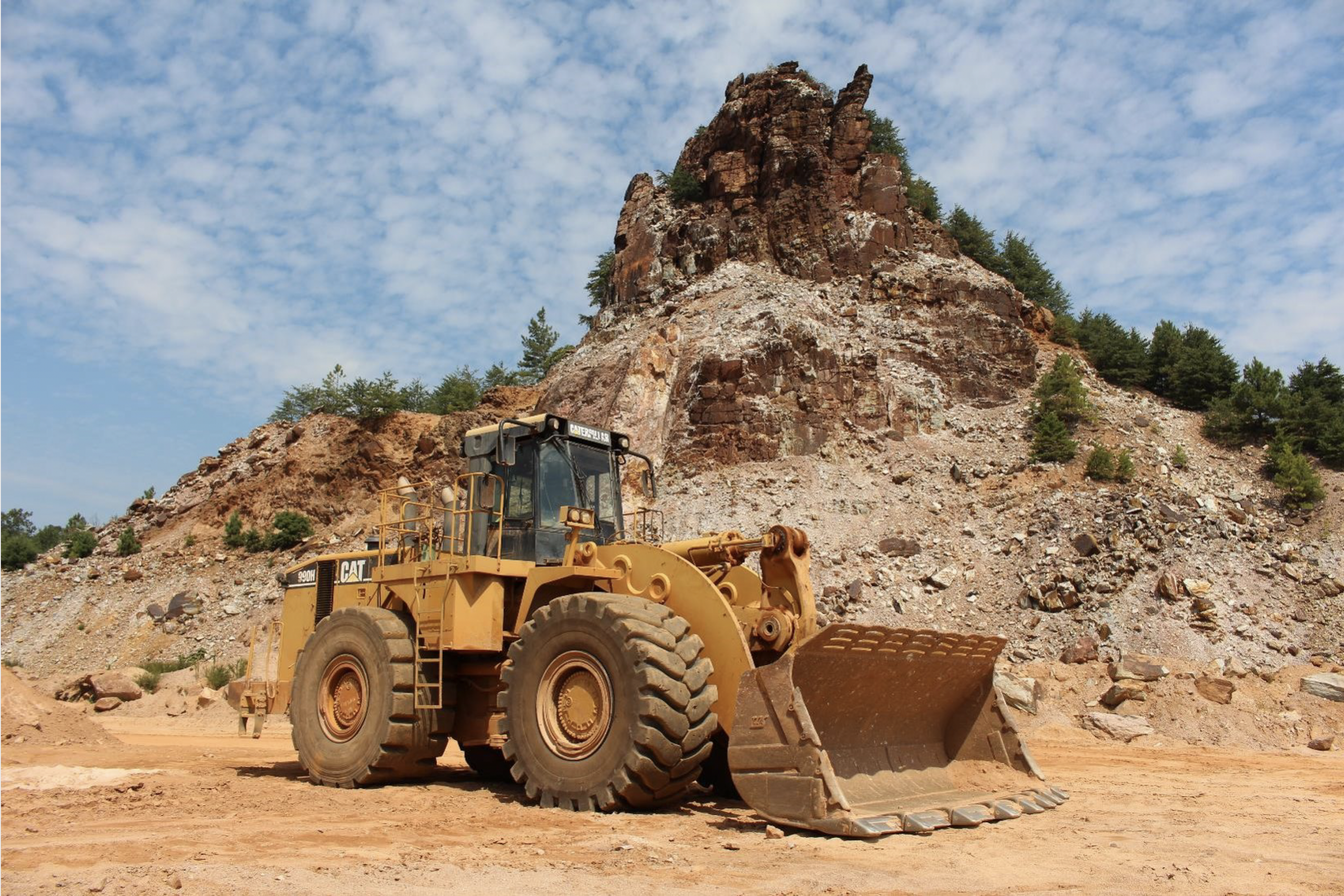
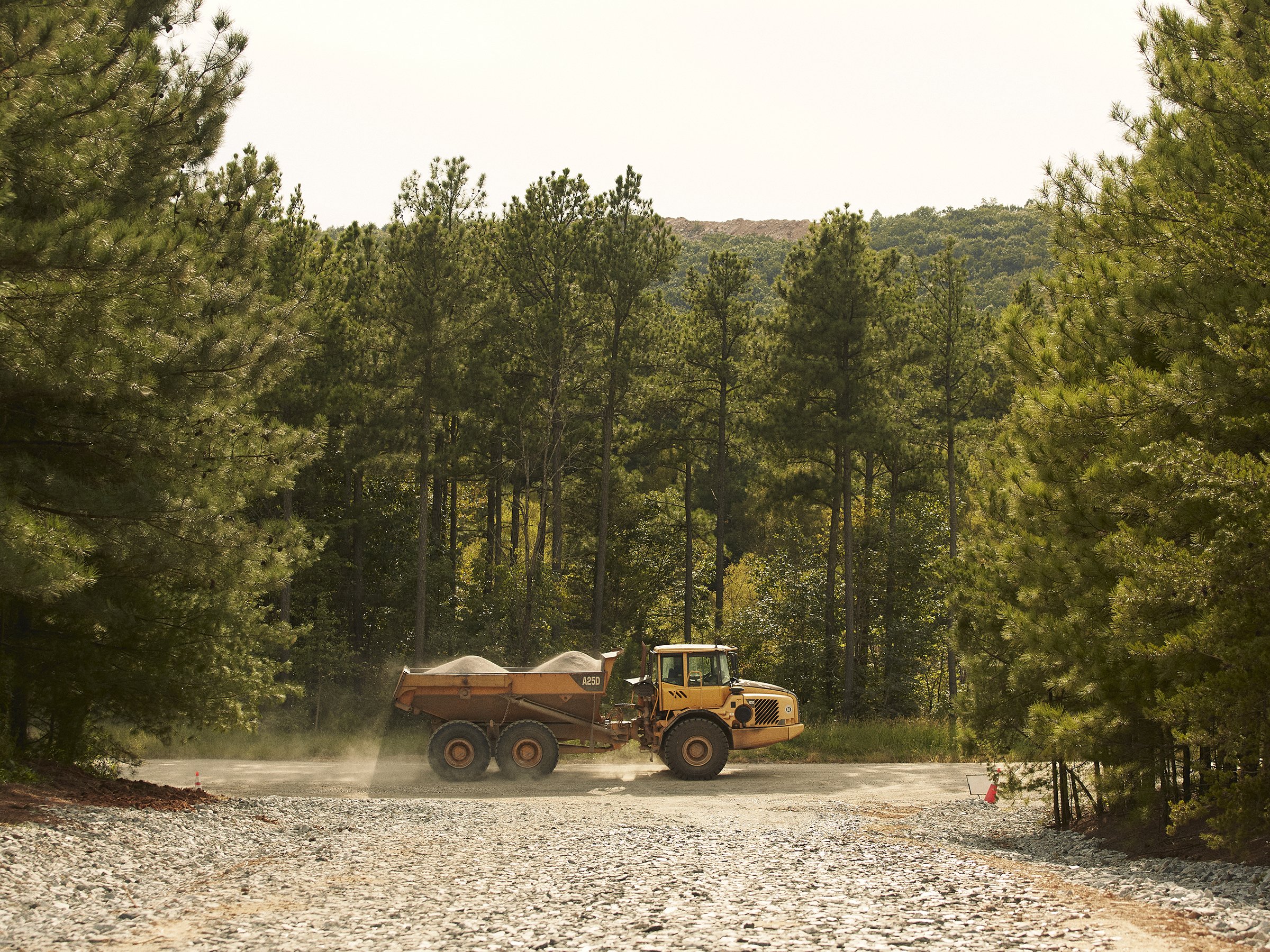
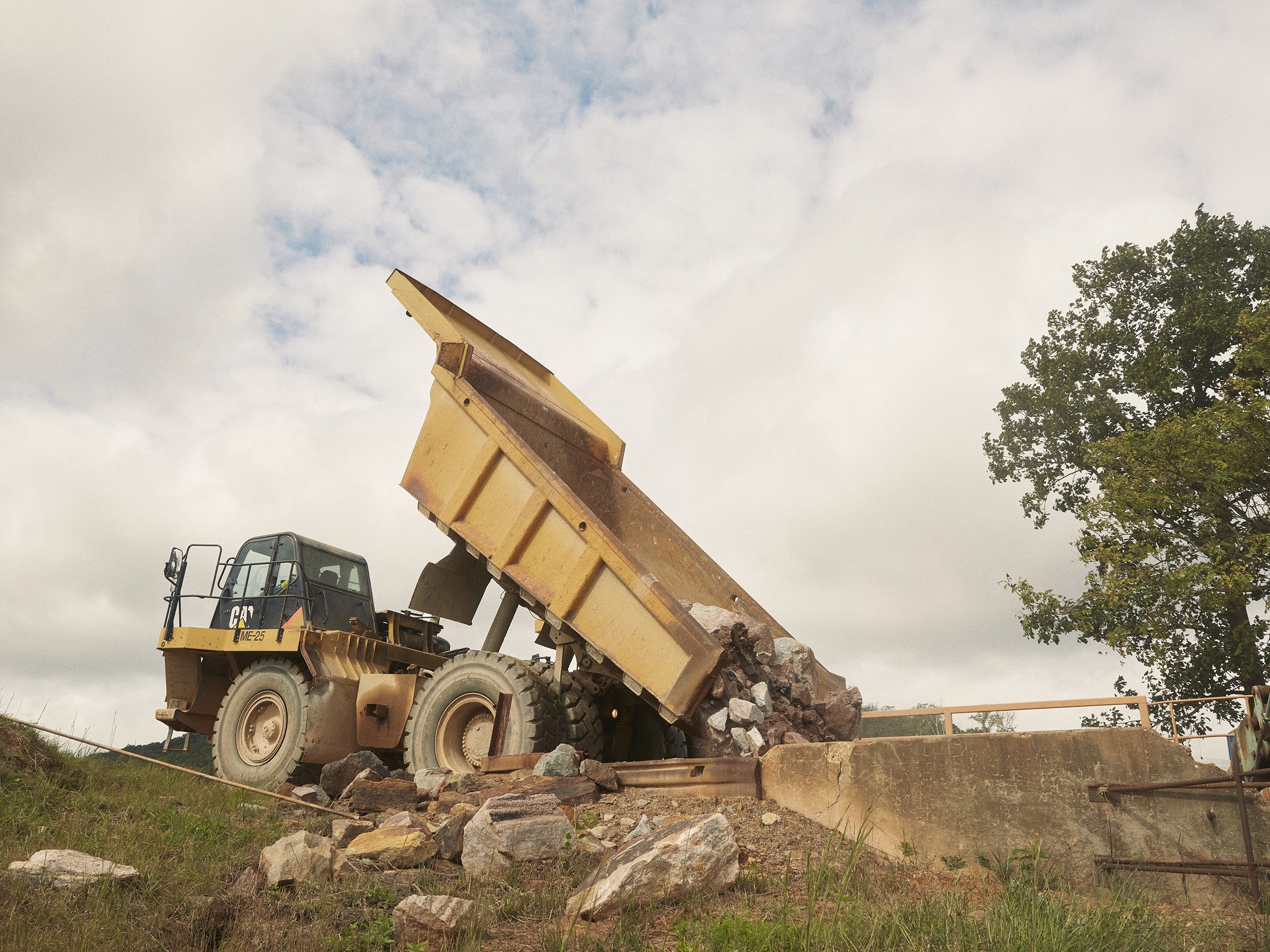
Mining
At Kyanite Mining Corporation, we invest for the long term by prioritizing the next generation over short-term gains. For this reason, we don’t perform “high-grading”–the practice of mining selectively and targeting high-grade areas of a mine while leaving lower-grade ore untouched. Instead, our mining process emphasizes extracting and blending material from different locations all over the Willis Mountain and East Ridge without following a vein. We utilize a fleet of trucks to haul and combine material from various spots in the mine together, closely monitoring ratios of blended materials to ensure consistency and quality.
Why mine from all over the mountain and blend all materials together? Significant differences of materials coming into the process complicate the purification processes, making life for the operators more difficult. We want to avoid variation as much as possible to yield the high quality and consistent kyanite concentrate that our customers rely on.
Quarrying occurs on a single daylight shift, five days a week, with blasting occurring 1-2 times a month at each deposit. Blasting is planned and supervised by an independent certified blaster. We drill blast holes, fill them with liquid explosives, and following strictly enforced safety protocols, hit the button. Following the blast, rocks too large to fit in our 50x60 inch crusher are broken down by a rock breaker. Loaders then load haul trucks, which transport the material for the next step in the process: comminution…
Comminution:
We use a large jaw crusher to blend ore from both quarries together and reduce the rocks weighing several tons (roughly the size of a pickup truck) to rocks weighing a few dozen pounds (roughly the size of a soccer ball). From there, the material undergoes several further stages of crushing and screening to progressively reduce the size of the ore to roughly one inch by down. Oversized materials that don’t make it past the screening undergo another round of crushing, until the material is uniform in size.
What’s in the Ore:
The average kyanite percentage of the ore is around 20%. This means roughly 600,000 tons of ore must be mined and processed each year to meet the 100,000–120,000 tons of annual demand for our purified kyanite and mullite products. We go to great lengths to remove the clay, soil, pyrite, mica, iron oxides, and quartz that represent the other 80% of the mined material.
Removing impurities from the raw kyanite is where we’ll pick up for the next part of our series…
Stay tuned!